View previous topic :: View next topic |
Author |
Message |
horse Member

Joined: Sep 08, 2019 Posts: 218 Location: Yorkshire U.K.
|
Posted: Tue May 14, 2024 10:41 am Post subject: Compression testing results. |
|
|
Last time out for a drive I noticed a noise which sounds like an air leak from say the Manifold or exhaust areas.
The noise is only when the engine is under load.
If you jack up the rear and run in gear no noise.
I checked all the manifold bolts and exhaust joints but couldn't find any blowby
Thought I would carry out a compression test.
I have never carried out a compression test before so working from TM 9-8014 page 74 I followed the instructions.
Only thing it does not mention is engine temperature but from another source I understand normal engine temperature required.
The manual reads normal psi 135 and the minimum 100 psi and should not vary more than 20%.
The results working from the front of the engine.
120psi 108psi 108psi 109psi
So a pass by the manual using the 20% variation but why do you think the first reading is much higher?
Your thoughts would be appreciated.
Horse _________________ 1952 M38 |
|
Back to top |
|
 |
wesk Site Administrator
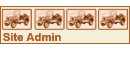

Joined: Apr 04, 2005 Posts: 16407 Location: Wisconsin
|
Posted: Tue May 14, 2024 11:46 am Post subject: |
|
|
The questions that you have brought up is why the compression test is not the final test. I would not question why the 120 is so high. The real question to ask is why are the other three 11-12 lbs. lower! You will find your answer in test #2. A leakdown test. This requires the use of a leak down tester. The unit allows you to apply a fixed rate of airpressure to a cylinder one at a time with the piston held at TDC on compression stroke. Once the pressure is applied the tester which has two gauges and a regulator shows the pressure going into the cylinder and the 2nd gauge shows the pressure being lost by the cylinder (pressure drop) caused by the cylinder's leaking problem. This is why the technical name of this tester is "Differential Compression Tester". Now the tester shows you definately have a leak but where you ask? This is where you revert to natural methods. Hearing being the most important. You simply listen for the air leak. You listen to the tailpipe to tell if the leak is thru a stuck or burned exhaust valve. You listen to the oil filler cap to hear if the leak is primarily across the worn rings. You open the radiator cap and listen and watch for the tell tale bubbles that will show the leak is thru the coolant system and head gasket. Finally you listen at the carb throat to hear if the leak is thru a stuck or damaged intake valve.
So I would suggest you move to step two and Google "Differential Compression Test" and "Differential Compression Tester" so you can ID the least expensive tester and understand the process clearly. _________________ Wes K
45 MB, 51 M38, 54 M37, 66 M101A1, 60 CJ5, 76 DJ5D, 47Bantam T3-C & 5? M100
Mjeeps photo album: http://www.willysmjeeps.com/v2/modules.php?set_albumName=Wes-Knettle&op=modload&name=gallery&file=index&include=view_album.php
Last edited by wesk on Tue May 14, 2024 12:26 pm; edited 1 time in total |
|
Back to top |
|
 |
horse Member

Joined: Sep 08, 2019 Posts: 218 Location: Yorkshire U.K.
|
Posted: Tue May 14, 2024 12:12 pm Post subject: |
|
|
Thank Wes.
Good point on the psi readings.
I will read up as you said on step two.
Seen a good video by Eric the car guy once the tester is hooked up.
As you said listen for the air coming out .
Will be interesting to see.
She does have the occasional put put on tickover on the exhaust.
Will return when I know more.
Horse. _________________ 1952 M38 |
|
Back to top |
|
 |
horse Member

Joined: Sep 08, 2019 Posts: 218 Location: Yorkshire U.K.
|
Posted: Thu May 16, 2024 6:47 am Post subject: |
|
|
While waiting for the leak down kit to arrive I thought I would see what the vacuum test gave.
So normal operating temperature engine on tickeover.
If a normal engine is between 17 and 22 inhg my reading is 18 inhg.
The needle does pulse at idle but steadies at increased rpm, which the manual indicates that the valve guides are worn or loose.
All the rest checks out okay.
Roll on the leak down test.
Horse _________________ 1952 M38 |
|
Back to top |
|
 |
wesk Site Administrator
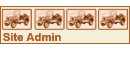

Joined: Apr 04, 2005 Posts: 16407 Location: Wisconsin
|
Posted: Thu May 16, 2024 10:42 am Post subject: |
|
|
Leakdown tests can be a wee bit difficult on automobiles but it is still the best choice to clear up compression reading questions. I grew up racing Ford flathead v-8's and small block Chevy v-8's in the late 50's - early 60's. Always used the standard compression check followed by that long lists of guess item checks and replacements. Then I got away from auto mechanic work when I got drafted and started working on turbines in heavy jets. Then I retired in the late 80's and started working small piston powered civilian aircraft and I learned the difference between the two tests very quickly. Seems in the old days with the 7 and 9 cylinder radial engines mechanics use to screw 7 or 9 compression gauges into the front spark plug holes and crank the old girl over and record all the readings then guess and swap to solve the bad readings. Then came the leak down tester and wow maintenance troubleshooting time was cut in half. The only big difference between auto and aircraft leakdown testing is on aircraft we can easily get the piston we are checking to TDC compression by just holding a fingerover the plug hole and pulling the prop blade around in circles. Cars present a tougher situation lacking the handy propeller for turning. It's a lot easier though with two folks on the car engines. Pull all the plugs. One guy holds his finger in the plug hole and the other guy rotates the fan in it's normal rotational direction while depressing the fan belt to improve friction. As the thumb guy announces pressure coming up on the thumb he quickly inserts a soft pencil like object in the plug hole and against the top of the piston and when the pencil stops coming up the piston is at TDC on compression. Now apply the air pressure and record the drop rate. A hint to save time is to just do each cylinder in the same order as the firing order and you won't have to make dozens of rotations on the crank. _________________ Wes K
45 MB, 51 M38, 54 M37, 66 M101A1, 60 CJ5, 76 DJ5D, 47Bantam T3-C & 5? M100
Mjeeps photo album: http://www.willysmjeeps.com/v2/modules.php?set_albumName=Wes-Knettle&op=modload&name=gallery&file=index&include=view_album.php |
|
Back to top |
|
 |
horse Member

Joined: Sep 08, 2019 Posts: 218 Location: Yorkshire U.K.
|
Posted: Thu May 16, 2024 12:01 pm Post subject: |
|
|
Thanks Wes ,very interesting on the aircraft radial engines.
I have been practising again on turning the crank with a socket and ratchet with all plugs out and placing my thumb over the spark plug hole waiting for the compression stroke to finish blowing. I also tried the pipe into a bottle of water method on the last stages of compression waiting for the bubbles to stop then just a bit more rotation and the marks line up forTDC.
Good tip to use the firing order to make it easier.
I know the pencil will not work on our engines but the thumb does fine.
I hope it is not the valve guides, been watching Metalshapers who has made a special hydraulic unit to remove them in seconds.
Also tonight on Wheeler Dealers Ant was doing a compression and leak down test on an old Toyota and showed your suggestions for listening to the air leaking out of the various areas.
Time will tell, thanks for the tips.
Horse _________________ 1952 M38 |
|
Back to top |
|
 |
horse Member

Joined: Sep 08, 2019 Posts: 218 Location: Yorkshire U.K.
|
Posted: Sat May 18, 2024 5:55 am Post subject: |
|
|
Hi, so the results are in on the Leakdown test.
Warm engine, thermostat open.
Cylinder 1 20% low ,air from Dipstick Exhaust Carb Throat.
Cylinder 3 20% low ,air from Dipstick Exhaust Carb Throat
Cylinder4 20% low, air from Dipstick Exhaust Carb throat.
Cylinder 2 20% low, air from Dipstick Exhaust Carb throat.
When you hook up 4 cylinder you get air out of 3 cylinder noticeable .
Not having done one before not sure how loud the air should sound.
All the Exhaust air are tiny only just hear it with ear on the Exhaust.
Carb throat a little louder..
Dip stick air all sound the same on each cylinder.
No bubbling from the Radiator.
I carried out the test about five times to check I was getting consistent results.
Any ideas?
Your input would be greatly appreciated.
Horse _________________ 1952 M38 |
|
Back to top |
|
 |
wesk Site Administrator
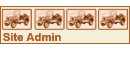

Joined: Apr 04, 2005 Posts: 16407 Location: Wisconsin
|
Posted: Sat May 18, 2024 10:56 am Post subject: |
|
|
20% is not bad just indicates an old engine. Noises that can be problems will be easily heard without holding ear close to noise exit port. Dipstick tube noise is the ring/piston blowby. Again if it is easily heard it means the blowby level is significant. Sometimes when piston rings inadvertantly have all their slots aligned it will cause an increse in blowby indications. Based on this:
#1 is fine.
#2 ? on it's 12PSI lower reading.
#3 ? on crossfeed with #4
#4 ? on crossfeed with #3.
3 & 4 are probably a head gasket issue or erosion between cylinders or valve seats or you have a couple of valves sticking open. Worse case a block crack between 3 & 4.
I'd start with a valve adjustment first. Redo the leakdown. If crossfeed still exists between 3 & 4 then pull the head. _________________ Wes K
45 MB, 51 M38, 54 M37, 66 M101A1, 60 CJ5, 76 DJ5D, 47Bantam T3-C & 5? M100
Mjeeps photo album: http://www.willysmjeeps.com/v2/modules.php?set_albumName=Wes-Knettle&op=modload&name=gallery&file=index&include=view_album.php |
|
Back to top |
|
 |
horse Member

Joined: Sep 08, 2019 Posts: 218 Location: Yorkshire U.K.
|
Posted: Sat May 18, 2024 1:52 pm Post subject: |
|
|
Thanks Wes, you have thrown me a bit of a life line.
Great break down of all the points.
At least I can try something then re test.
If you have sticking Valves as you can see the top of the valves through the spark plug holes ,would there be any benefit to spraying penetrating oil onto them?
Or is that a bad idea?
Thanks.
Horse. _________________ 1952 M38 |
|
Back to top |
|
 |
wesk Site Administrator
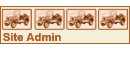

Joined: Apr 04, 2005 Posts: 16407 Location: Wisconsin
|
|
Back to top |
|
 |
wesk Site Administrator
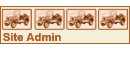

Joined: Apr 04, 2005 Posts: 16407 Location: Wisconsin
|
|
Back to top |
|
 |
horse Member

Joined: Sep 08, 2019 Posts: 218 Location: Yorkshire U.K.
|
Posted: Mon May 20, 2024 11:38 am Post subject: |
|
|
Thanks Wes ,back on.
Horse _________________ 1952 M38 |
|
Back to top |
|
 |
jimm Member

Joined: Nov 01, 2011 Posts: 202 Location: Escondido, CA
|
Posted: Tue May 21, 2024 7:05 pm Post subject: |
|
|
This is a great "test and probable cause per test results" thread. I learned long ago, starting with my M38 that I bought in 1978, that you can learn a lot of things from a vacuum gauge that a compression test won't reveal. Ditto for the leak down test, but I'll admit I haven't done on of those.
My neighbor and I both have equipment with air-cooled Wisconsin V-4 flathead engines, on concrete saws and a brush chipper, respectively. Lots of similarities to the Willys L134, which is why, in combination with my neighbor's long experience with them, I was comfortable buying the chipper this even though it would only crank but not fire and run. Turned out to be a basic ignition problem and it ran great after fixing that. Anyway, the discussion of sticking valves reminded me of an issue he had on one of his saws which had an engine built in the dying days of Wisconsin production. When he tore it down, he found that several of the valve stems had virtually no clearance within the guides! (Minimum clearance spec on that engine is 0.003") One of them we had to work out with a pry bar! The valve guides were under minimum spec diameter, which means they left the factory that way. He reamed them to spec and all was well and the engine runs great now. Unlikely to ever encounter that on an L-134 but it just goes to show that 1) you never know what you're going to find, and 2) correct evaluation, diagnosis and repair will get you where you want to go. _________________ Jim McKim
1952 M38 son-father project
Slowly turning rusty parts into OD parts |
|
Back to top |
|
 |
horse Member

Joined: Sep 08, 2019 Posts: 218 Location: Yorkshire U.K.
|
Posted: Thu May 23, 2024 11:33 am Post subject: |
|
|
Thanks jimm interesting story which leads me on to more information on my engine.
So I adjusted the Tappits to 16 Thou as per the manual using both my thumb to find TDC on each cylinder and the magic 9 method. Some did need a little opening out.
I carried out another leak down test with better results this time.
Cylinder one 20% low Dipstick noise only.
Cylinder three 20% low Dipstick noise only.
Cylinder four 20% low Dipstick and Throat.
Cylinder two 20% Dipstick noise only.
No noise from the exhaust and no bubbling from the Radiator.
All the cylinders sound the same down the Dipstick.
No crossfeed this time which is good.
So while she was warm I did another Compression test.
120psi 110psi 110psi 115psi again a little better.
Once back together I still have the air type noise.
I will try to record this.
Thanks for your input Wes, good call on the Tappits.
Horse _________________ 1952 M38 |
|
Back to top |
|
 |
horse Member

Joined: Sep 08, 2019 Posts: 218 Location: Yorkshire U.K.
|
Posted: Sat May 25, 2024 8:28 am Post subject: |
|
|
Result, just found an air leak.
I did notice when looking around the joint on the down pipe next to the manifold a little bit of black blow by ,but could not feel it with the engine running.
Any way just put a low pressure air line up the exhaust and sure enough an air leak.
I will take it off and get it welded up.
Good little project for me as I have learned a lot in test procedures and
have improved the cylinder pressures with Tappit adjustments.
I know the engine is a little worn but will run a little longer yet.
Thanks for your help.
Horse _________________ 1952 M38 |
|
Back to top |
|
 |
|